I would only do this for you guys!
The first photo shows the complete knife disassembled and the parts layed out. Note the rear view. This shows the pommel nut in place. The sleeve that it fits into is a 3/8 diameter stainless rod that has been turned and drilled on my lathe to have an internal "shelf" for the pommel nut to catch as it is threaded onto the tang. This pulls everything forward toward the guard shoulders and brings the entirety of the handle materials into one integral unit from the tip of the blade to the butt of the handle.

Second photo shows the front end. Now, those pins are 1/16th hardened pins that connect the handle material to the guard. This accomplishes numerous things:
.... it prevents any lateral movement of the handle material or twisting. It also allows me to repeatedly assemble and disassemble the knife durings its creation.
....As well, when the knife is not in use and is lonely in the gun case, you loosen the pommel nut and let the handle material move however it wants without creating any stresses.
....I do a lot of hot bluing and this allows the owner to keep everything lubed and oiled up to prevent oxidation as well as allows me to re-blue if necessary in years to come.
The slot in the handle is filed to fit the tang. Even without the pins, the knife would be functional.
The guard is tightly fitted.
I make many fixed-assembly knives as well, yet they are ALL assembled in the same manner with pins and a pommel nut through the rear. In the fixed assembly, I simply eliminate the sleeve and drill a hole in the handle the same size as the pommel nut. I place an interal washer into the hole to catch the shoulder on the pommel nut so as not to wear against the handle material.
Does this help? (Don't forget last picture)
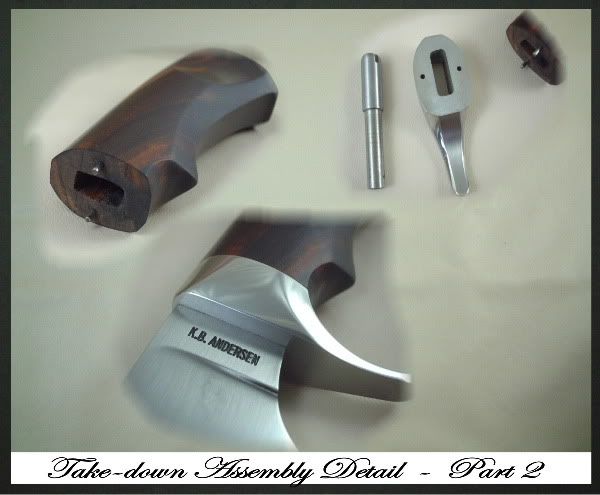
This shows a fixed assembly knife:
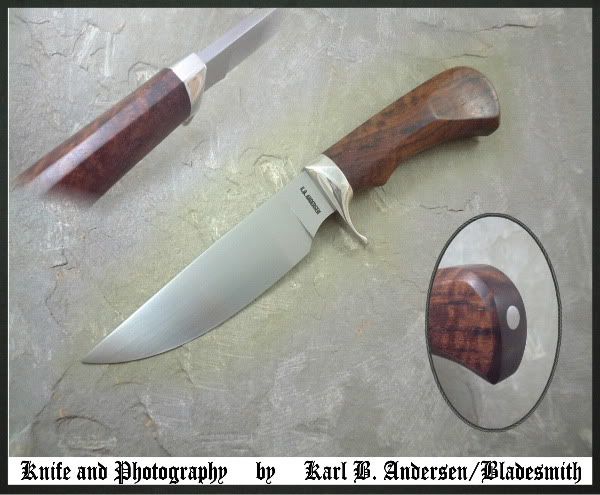