Here is what I've been working on the last couple of days. I decided I wanted a small knife that would be comfortable on a belt for general light duty around camp. So I made two.
The first:
5" LOA
5160
Muriatic acid etch
Brass pins
Big Leaf maple burl
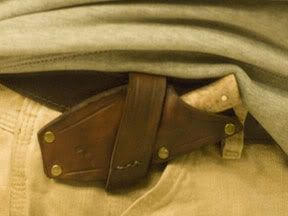
I wanted a sheath that was comfortable when you sit down... so I changed some of the horizontal sheaths I've seen and made it sit diagonally on the belt. Very comfortable. I'm wearing it right now and I'm tickled by it. I also tried just using rivets instead of stitching thinking that "Why not let a blade breath?"
Anyway... I love this knife and it's my favorite that I've made so far. It passed my brass rod test with flying colors (if I'm even doing it right). But... no blade deflection or chipping.
The second:
Another piece of sawmill steel that Kevin gave me.
5.5" LOA
Unknown sawmill steel
Deer antler bolster
red spacers
Birch bark
Big Leaf maple burl
Copper lanyard tube
rope? file work

This one is a little fancier than I like... But I figure if you are gonna learn the whole craft, sometimes you have to get fancy I guess.
This one got some pretty serious pits during the quench. I couldn't sand em out because I had little enough blade left as it is. Anybody know what can be done about pitting during the heat treat? I used my ceramics kiln and brought it up to 1500 for 10 minutes and quenched in vegetable oil.
Anyway... Grinding is still a challenge and I'm having the problem of losing alot of material through mistakes... especially at the ricasso/plunge area. But I guess this is what it is at my stage.
Tear em up boys!