banana 4 fletch using a modified lil chopper banana high profile feather chopper (a new base plate was made from 1/8" plywood, in order to shorten the fletch length, and reduce the height), place the feather into the jig and hold it with a few fingers. notice that i prefer to chop feathers with the 'concave' side of the feather up ...
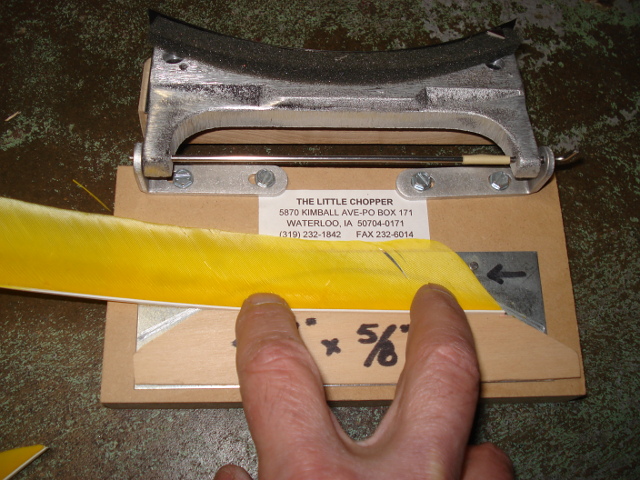
holding onto the feather, use yer other hand to lower the chopping blade and hold firmly enough so the feather won't move ...
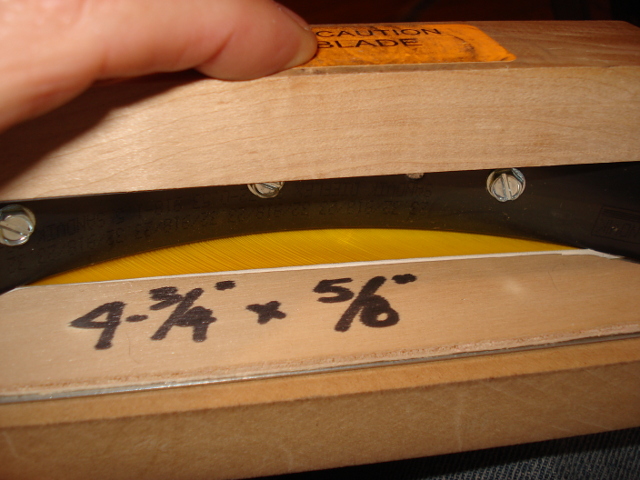
give the blade block a good, sharp whack with a mallet or hammer ...
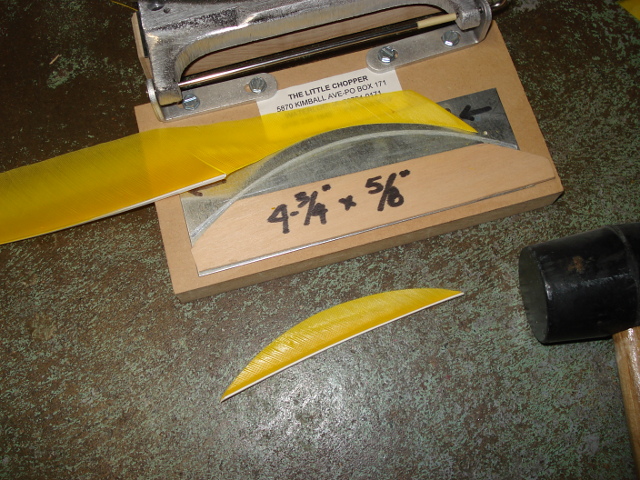
as mentioned b4, the nock can be pushed on for a friction fit during fletching and then aligned and glued later, or glued on first - i choose to glue on first because my jig's nock receiver is well set up for an offset 4 fletch.
after wiping down the cap area of the shaft (where the fletches go) with naphtha (lighter fluid) on a paper towel to remove any finger oil, i've placed a fletch into the fletch jig's clamp, and i'm doing a 'test run' to make sure the fletch quill will position itself properly on the shaft and that it's the proper distance from the nock.
you will need to spend a bit of time and effort to tweak the clamp so that the fletch lies well on the shaft. with a straight fletch clamp, it is either set dead straight (not recommended), slightly offset in the direction of the fletch (i.e. - left wing feathers are offset to the left side). if a helical clamp is used, take extra care in making *sure* that the entire base quill of the fletch makes contact with the shaft. if you don't get the fletch quill to lie dead against the shaft, you will have problems. this matters for using either fletch tape or glue - so make this an important priority! when it all looks good, mark the clamp with sharpie pen where the back end of the feather goes, for consistency (i used a black pen mark for this fletch type) ...
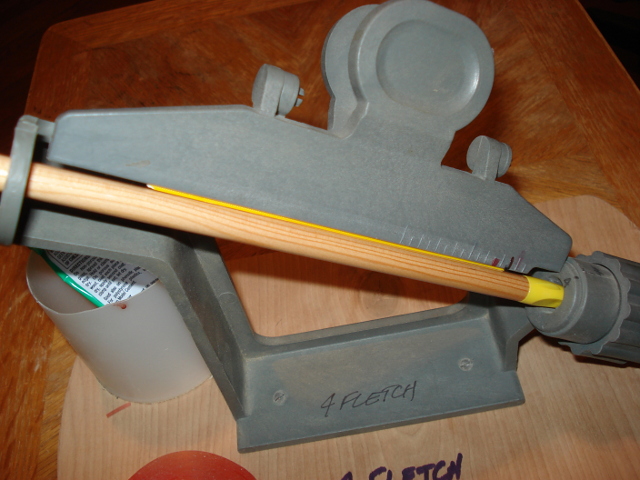
when all looks right, remove the clamp (with feather attached) and at this point i typically will wipe down the quill base with naphtha on a piece of paper towel to remove any lingering finger oil, line up the fletching tape with the quill base and lay it down ...
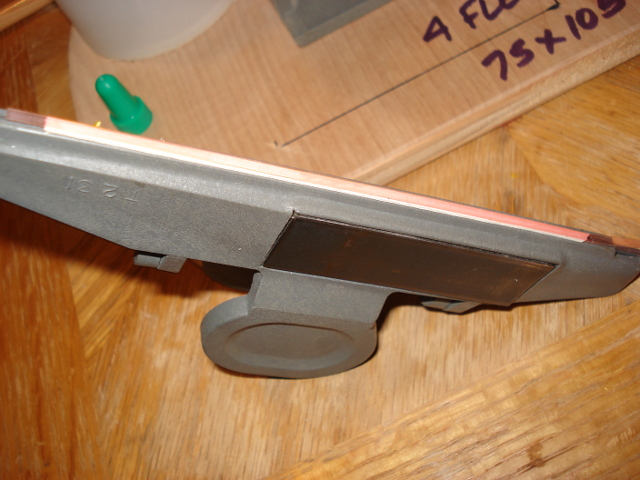
with sharp scissors, snip off the tape at both ends of the fletch, close to the quill ...

run a finger down the length of the fletch tape, pressing fairly hard - do it again to be sure ...
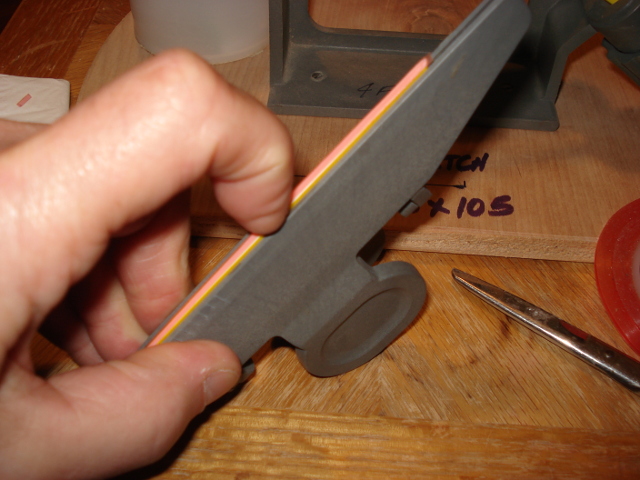