This is the third one of these knives I've been asked to make this year so I thought I might document a few of the steps, including a new method I devised to secure my fixed blade stag handles.
Unless it's a really interesting pattern, the manufacture of Damascus is something most of us have seen many, many times, so I'll dispense with that.
This blade is a 324 layer laddered random of 1095 and 15N20.
(She will be hot-blued this afternoon, as well as the twist fittings!)
This is a rough overview of the knife:
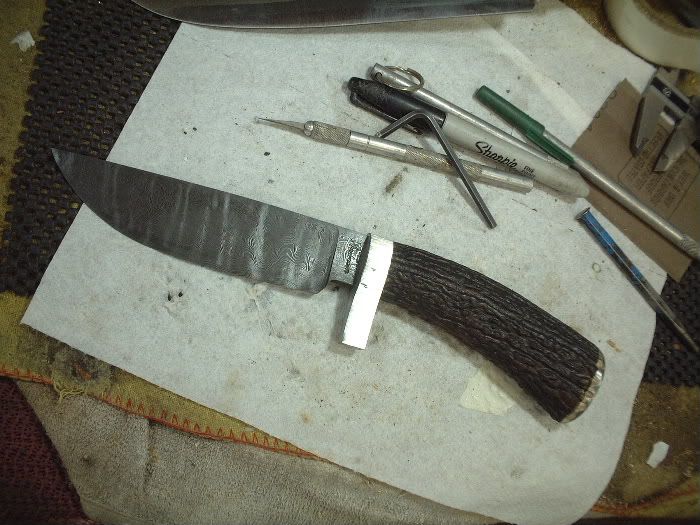
A couple fit-up photos:
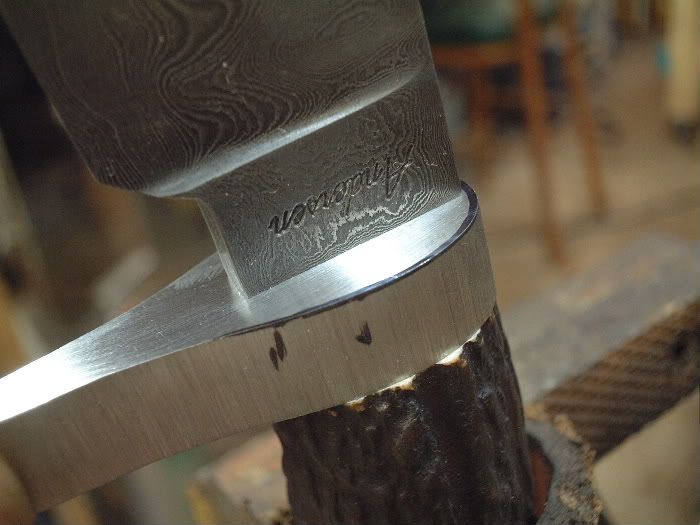
Guard is pinned to handle and then shaped toward it's final dimensions:

I am a true stickler for having ALL of my handle and hardware parts pulled FORWARD into the guard shoulders. I machine all of my surfaces, including the face of the handle material, so all surfaces mate up with zero tolerance. I take advantage of that with tension from the rear to integrate all pieces into one physical unit.
Amazingly strong that way.
I finally came up with a way to fully tighten the fixed assembly stag handle into one unit as I just described.
I took a long shank end mill and cut two "STEPS" into the top and bottom of the void in the middle of the stag taper. I did this about 1" in from the butt end.
Across these two steps, I placed a stainless "BRIDGE" with a hole in the center, through which I place my 10-32 finial.
The finial is a stainless rod with a step milled in, so as to catch the hole in the "BRIDGE".
Into the butt of the finial, I have threaded and silver brazed a stainless socket head cap screw.
Now I can pull that handle and guard smack TIGHT up to the guard shoulders.
It makes me happy when I can do that.
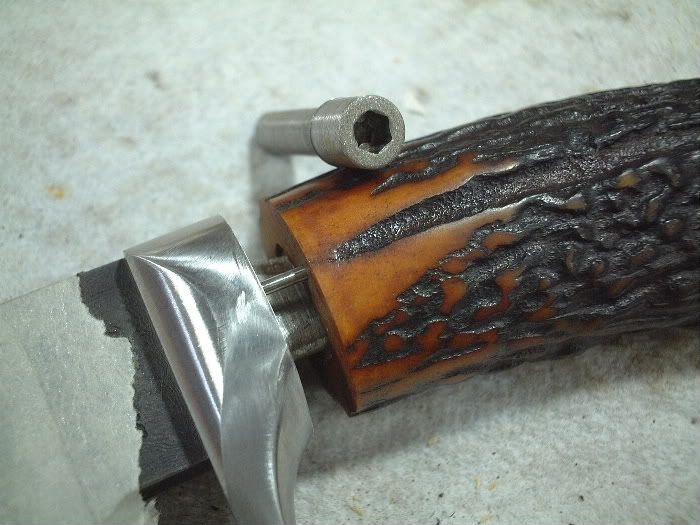