I will admit that this has been a while coming, and something I have been working on for, maybe, two years?
It's just not easy to do, and having finally figured out all the complexities that are involved with the way I do things, the materials and my equipment, I just really wanted to share this you guys.
The difficulties include the fact that stainless steel just does NOT want to weld to tool steel very well. There come these few moments during the creation, welding, forging and heat treating segments that literally bring into play everything a maker has learned - up to that point.
And there is zero tolerance for failure.
But, the results are quite dramatic.
What we have is a three piece sandwich - a 1095 tool steel core with a layer of 416 stainless steel laminated to the sides for corrosion protection - and it just looks kind of cool!
Some neat carbon migration going on, raw iron exposed, etc.
I'm excited to finish this one out - my first one of 2012!
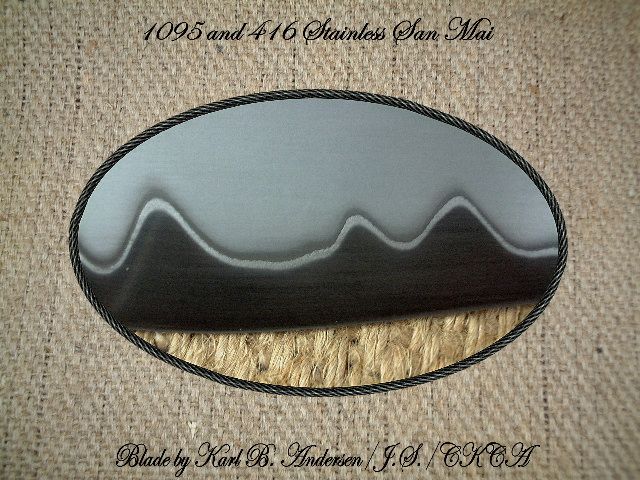