I'm a lurker on here and admire the craftsmanship that is displayed. I've put some handles on purchased blades and even participated in one of the knife swaps, but have never forged a blade -- until now. At the risk of boring the pros on here, I'm going to try to relate my experience. This will take me a while to get it all posted so hang with me!
Steve Auvenshine lives just down the road from me and occasionally puts on knife making seminars. My wife (I love that woman) gave me the seminar for our anniversary last year but due to Steve's schedule he didn't have a seminar until Memorial Day weekend. He takes a limited number of students for a weekend and you forge a knife and walk away with your completed project. Steve was an apprentice with Frank House and does a lot of work for Hollywood. There's lots of knowledge and tools available to do what needs to be done.
My friend Skip also attended this session so with only two of us, there was lots of one-on-one time.
We started Friday night with the forging of our blades. Skip had attended a previous session so he was an old hat at this. I went in with the idea that I wanted to make a larger version of one of my current knives that I like. I've got one of the little Marbles Capers that I really like for field dressing and wanted something a little bigger. Steve and I sat down and drew out a rough pattern and got to work.
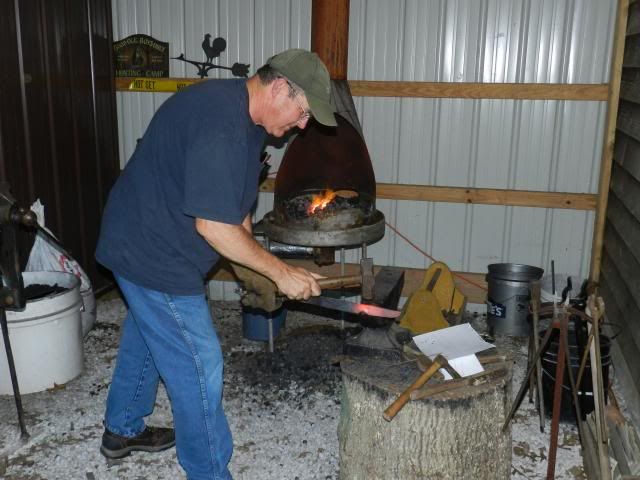
Here I am shaping the blade. If I remember correctly, we started with a bar of 1085 as the raw material. The material was pretty thick so we determined that I would need to have a tapered tang to help with weight/balance and to keep the strength.
I had seen you guys mention it on here before but it was very interesting to me to observe first hand that when thinning the blade, it wants to curve backwards. I would have thought it would be the opposite.
I left Friday night with my blade sitting in the ash bucket to cool slowly so that I could start shaping on Saturday morning.
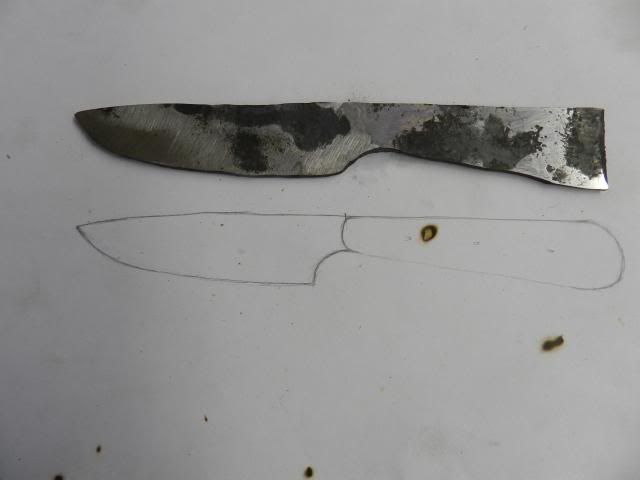
Here's what I pulled out of the ashes Saturday morning.
More to follow