OK, I've got a really tough arrow but I'm wondering if I could build it even better. I'm currently using carbon shafts with aluminum footing, then I use a 1 piece brass adapter to mount a big single bevel BH. All is well, it shoots great, I get great penetration, etc. I don't have to change anything.
What I'm wondering is this: currently my brass adapter is about 1 inch into the shaft and ends on an abrupt line. With this setup it breaks when I shoot plate steel targets during destructive testing right at the end of the adapter. I've started footing over the shaft with aluminum in an attempt to transfer more energy before hitting the breaking point. Now I do believe it hit's harder, but it usually snaps at the end of the footing in a clean line. Better but not ideal.
What I'm considering is this: what if I put something like purple heart on a lathe and made the section glued to the carbon something like 3" or 4" long, and tapered the end so there wouldn't be an abrupt line to snap the carbon on? What I'm picturing would be something like this.
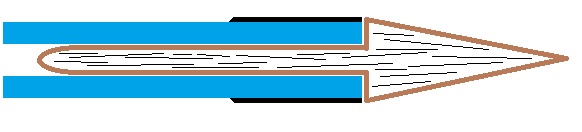
Of course the BH would cover the wood and go cleanly over the aluminum footing as it currently does.
Have I gone crazy in all my time testing and destroying arrows, or am I on to something here? I really think that slow internal taper would give a lot more flex before breakage, but if anyone has done testing like this I'd love to know their results.
Thom